Kentucky Employers’ Mutual Insurance (KEMI) announces the induction of Robert (Bob) L. Swisher into the Class of 2025 Kentucky Workers’ Compensation Hall of Fame.
Bob Swisher, one of five inductees, was recognized in April during the Kentucky Workers’ Compensation Hall of Fame Banquet, which honored those who have made significant contributions to the Kentucky workers’ compensation system throughout their distinguished careers.
Swisher began his law career in 1979 after graduating from the University of Kentucky College of Law. With over 10 years in general practice, he joined Geralds, Moloney and Jones concentrating on civil litigation, workers’ compensation, and probate law before joining the workers’ compensation defense firm Jones, Dietz and Swisher in 2007.
On January 1, 2010, Swisher was appointed as an administrative law judge (ALJ) in the Kentucky Department of Workers’ Claims (DWC) by Governor Steve Beshear. In 2013, he was one of two ALJs selected to participate in the DWC’s new medical dispute resolution program, and in 2014, he was named chief administrative law judge.
Swisher was appointed commissioner of the Kentucky DWC by Governor Matt Bevin in 2017. During his tenure as commissioner, Swisher led the agency through full implementation of the Litigation Management System, the online filing and case management system created by former Commissioner Dwight T. Lovan. Responding to legislative mandates in House Bill 2 (2018), Swisher promulgated numerous regulations, including the adoption of workers’ compensation medical treatment guidelines and a pharmacy formulary, creation of the process by which injured workers may apply for a continuation of medical benefits past 780 weeks, and the creation of an online portal through which coal miners awarded retraining incentive benefits locate and select an institution to provide their retraining.
In 2021, Swisher joined KEMI as director of Claims-Legal. In this capacity, he oversees KEMI’s in-house legal manager, the Special Investigations Unit, the Medical Bill audit unit, and KEMI’s Claims business analyst.
Swisher is a member of the Southern Association of Workers’ Compensation Administrators (Adjudication Committee), was selected as a Fellow in the College of Workers’ Compensation Lawyers (2018) and was a finalist for the 2019 Comp Laude Award as a national industry leader.
“This recognition of Bob’s contributions to the workers’ compensation industry is well-deserved,” stated KEMI President & CEO Jon Stewart. “Employers and workers throughout the commonwealth continue to benefit from Bob’s vast knowledge of workers’ comp and unwavering integrity that guides each decision.” Stewart continued, “But beyond his career accomplishments, Bob is a man of character and one of the finest individuals you could ever meet.”
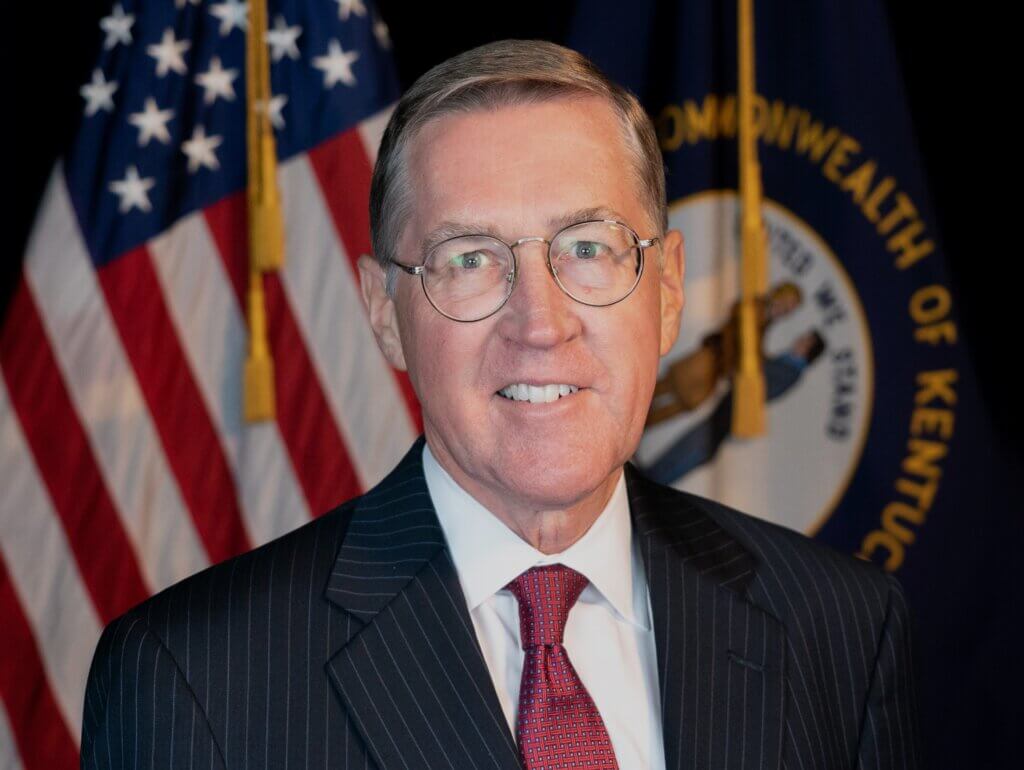